如何打造一条环保的机制砂生产线?3个案例告诉你答案
发布时间:2020-03-10
目前,随着各地矿山石料需求的增多,越来越多的矿山企业老板开始扩大生产规模以提高产量,因此选择合适的成套机制砂生产线成为矿山老板的重要任务。但您知道如何打造一条环保的机制砂生产线吗?
今天小编分享几个典型案例,分别介绍其工艺流程及特点、设备选型等内容,从而对机制砂生产线设计的要求、需要注意的问题等方面给出一些可行性建议,供您参考。
一般来说,机制砂生产线系统一般包括几个单元:①初碎单元、②半成品储料单元、③中细碎单元、④筛分单元、⑤成品储料单元、⑥装车秤量系统、⑦给水及水处理单元、⑧电气自动化系统、⑨备件及维修中心
一个好的系统要做好以下几方面的工作:
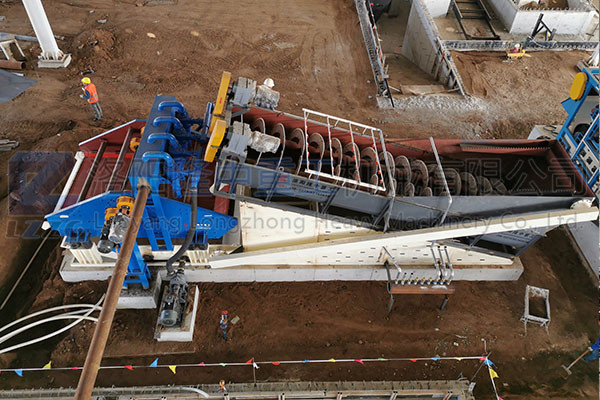
①安全:比如场地规划;设备维修操作的安全空间设备上方设起吊装置;场地规划检修通道;皮带廓及各楼层设人员通行的走道及梯子。
②环保:采用闭路水循环系统及污水处理系统,污水实现零排放;厂内所有扬尘点设g效除尘设施;场内道路及地面硬化处理。
③高自动化程度:系统通过采用编程控制实现全自动运行,除特殊情况下,无需人工干涉;系统能自动做出故障诊断和相应处理,并发出报警信息供操作人员解决。
④维修保养方便,设有专门的备件库存及维修中心。
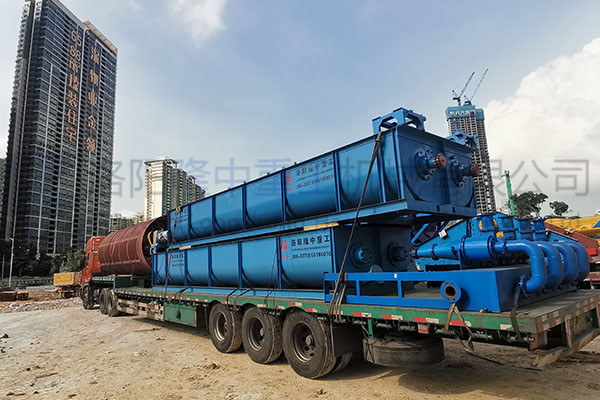
⑤节能:采用低耗能设备;对于生产过程中需经常调节介质参数的设备,采用变频调;变电所尽量靠近用电负荷中心位置等等。
一、石灰岩等较软及较低磨蚀性的机制砂加工系统工艺
该工艺是目前大多商品机制砂加工系统的典型工艺,工艺简单,设备配置少。
粗碎采用棒条给料机,棒条给料机具有均匀、稳定给料和筛分的功能;棒条筛上物进入颚式破碎机破碎,提高破碎机的生产效率同时降低衬板的磨耗。根据料源情况,棒条筛下物可随粗碎后的骨料一同进入调节料堆,也可以进入除泥筛分机进行除泥,在粗碎前除泥,可以大大减少有用料的浪费且达到除泥的目的。
中碎之前一般设置调节料堆,由于汽车运输的不连续稳定,调节料堆可确保后续工艺在一定时段内连续稳定生产,提高设备的利用效率,同时当粗碎临时检修或处理c径石时,后续工艺受到影响不大。
中碎采用反击式破碎机,破碎后的骨料进入预筛分车间,其中满足规格的骨料分别进入成品骨料堆,c径骨料进入细碎车间,其余进成品筛分车间进行筛分,满足要求的成品骨料进入成品骨料堆。
二、花岗岩、石英岩等较硬及较高磨蚀性的机制砂加工系统工艺
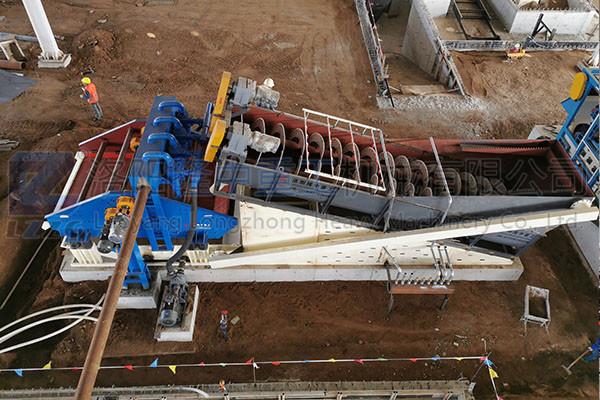
该工艺主要利用圆锥破碎机的“层压破碎”原理,成品粗骨料通过两段圆锥破碎后,得到更好的粒型。
与一的工艺流程中,中碎前段的破碎筛分处理工艺相同,中碎及后序工艺有所不同。中碎后的骨料进入预筛分车间,通过预筛分将小于5mm 的细骨料筛分出,全部粗骨料进入细碎车间进行破碎,通过细碎后的骨料再进入成品筛分车间,其中满足规格的骨料分别进入成品骨料堆,c径骨料进入细碎车间。细碎车间设置调节缓冲仓,当相关的主机或其他设备出现故障紧急停车时,料仓可以起到储料的功能,减少主机停车后满腔和皮带机带负荷启动的风险,同时料仓的调节作用可以让细碎腔满给料,使成品骨料粒型更好,设备磨耗更低。
粒型较好的骨料可以减少水泥等用量,增加和易性,减少泵送混凝土堵管道的机率,降低混凝土搅拌站的成本;同时也可增加混凝土的强度,这也是为何高标号混凝土对粗骨料的粒型有严格控制的原因。
该工艺中将中碎后的细骨料筛分出而不进入细碎,主要原因是:细骨料含量过多将填充粗骨料之间的空隙,降低细碎的破碎效率,同时在满给料的情况下容易导致细碎设备闷腔而损坏设备,降低细碎设备的使用寿命,预筛分的工艺措施可消除这种隐患。
三、普通商品骨料含制砂系统工艺
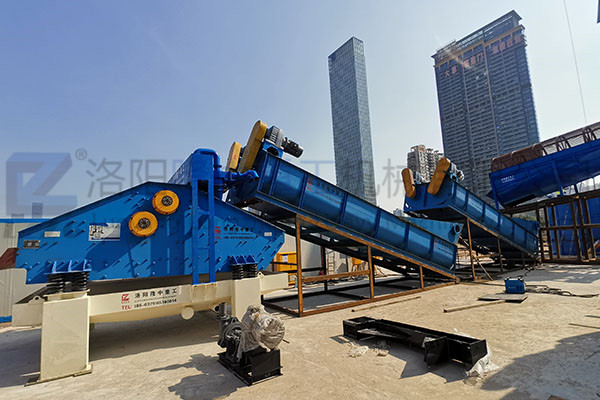
砂在商品混凝土骨料中的比例一般在30%左右,用量相对较大,对于目前天然砂资源的枯竭和限制开采的环境下,人工机制砂逐渐成为趋势和主流(目前大型水电站建设主要采用的是人工机制砂)。
目前机制砂主要是采用立轴冲击式破碎机,由于立轴冲击式破碎机具有整形和破碎的功能,因此制砂的工艺也相对较多,有立轴专制砂而不出粗骨料,有的制砂工艺兼顾对粗骨料进行整形,该工艺就是制砂的同时兼顾对5-10mm的骨料进行整形(也有的工艺兼顾对所有粗骨料进行整形)。
该案例中:中碎后的骨料和细碎后的骨料进入成品1筛分车间,筛分出10-20mm、20-31.5mm的成品粗骨料,其中部分10-20mm和20-31.5mm的成品粗骨料以及全部5-10mm的骨料进入了了制砂调节料堆。通过立轴冲击破碎机破碎和整形后进入成品2筛分车间进行筛分,大于10mm的骨料全部返回制砂调节料堆,形成闭路循环,部分多于的5-10mm返回制砂调节料堆形成闭路循环。在该案例中,为了调节成品砂的细度模数(调节砂的J配,一般采用的是中砂),筛分后大于3-5mm的部分骨料返回制砂车间形成闭路循环。